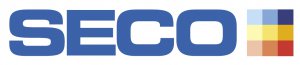
Цех обработки стремится производить определенное количество деталей, а также обеспечивать требуемое качество, максимальную эффективность работы и своевременность поставки. Традиционно производственные предприятия оценивали эффективность по окупаемости инвестиций. Успех определяли с точки зрения непрерывной работы тысяч или сотен тысяч единиц оборудования, а цель заключалась в поддержании стабильной производительности одного или нескольких станков. Согласно такому подходу станок считался эффективным, если работал без перебоев и обеспечивал изготовление деталей.
В настоящее время распространено мелкосерийное производство широкой номенклатуры в соответствии с конкретными требованиями каждого клиента. Размер партии может варьироваться от единиц до сотен деталей. Однако в некоторых случаях клиентам все равно приходится ждать заказанные детали, даже если все станки на предприятии работают непрерывно. Стратегии крупносерийного производства вступают в противоречие с требованиями гибкости и сложного планирования, которые характерны для мелкосерийного производства.
В существующей производственной среде эффективность подразумевает достижение гибкого баланса между максимальной производительностью и своевременным выполнением разнообразных заказов по индивидуальным требованиям клиентов. Важен конечный результат: своевременная поставка продукции и удовлетворенность клиентов.
Контроль качества
В поиске баланса между производительностью и спросом производителям необходимо помнить о качестве продукции. Использование деталей недопустимого качества становится причиной незапланированных изменений в графике производства, потери времени и средств, а также задержки поставок. Недостаточно тщательное планирование приводит к остановке производства, простою станков и росту затрат на рабочую силу в цехе, поскольку необходимо устранить непредвиденные проблемы, возникшие в результате остановки производства.
Качество заготовки в производственной сфере обычно описывают с точки зрения соблюдения требований к размерам детали и шероховатости поверхности. Дополнительным параметром оценки качества является своевременность поставки. Производителю необходимо контролировать технологические процессы, чтобы выделить достаточное время для работы и поставки клиенту в соответствии с обещанным сроком.
Figure 1:
HQ_ILL_Total Quality.jpg
Удовлетворенность клиентов или прибыль?
Предприятие может использовать станки 100% времени, но если при этом оно не обеспечивает своевременную поставку, это приводит к потере клиентов и убыткам. Удовлетворенность клиентов — это основная цель, но если производитель концентрирует усилия только на этом, прибыльность предприятия может снизиться. Клиентоориентированность имеет решающее значение, но производителю также необходимо максимально эффективно использовать оборудование, изготавливать необходимый объем деталей, обеспечивать требуемое качество и своевременную поставку продукции.
Обязательства и планирование
Успех производства зависит от организованного взаимодействия нескольких групп в пределах организации. Одна группа договаривается с клиентами о затратах, качестве и времени поставки заказываемых деталей. Другим группам организации (инженеры, специалисты по закупкам, персонал мастерской и администраторы) предстоит выполнить оговоренные обязательства.
Каждая группа определяют эффективность по-разному. Специалисты по обработке хотят оптимизировать отдельные процедуры для достижения максимальной производительности. Группы, которые не задействованы в технологическом процессе обработки, стремятся повысить общую производительность системы. Они анализируют аспекты, к которым в том числе относятся общая эффективность оборудования (OEE) и производительность труда.
Сердце эффективности
Говоря фигурально, обработка является сердцем любой производственной операции. И хотя этот орган является ключевым, он не может работать абсолютно самостоятельно. Сердце — это элемент системы, которая включает в себя головной мозг и другие органы.
Если в производственном процессе функции сердца выполняет технология обработки, то телом является все предприятие, в которое входят инженерный отдел, отдел бизнес-планирования и администрация. Головной мозг организации — это группа сотрудников, ответственная за координацию всех элементов системы. Однако головной мозг не может просто решить, что сердце должно работать быстрее, — человек не может контролировать свое сердцебиение с помощью мысли. Точно так же не всегда удается рационально управлять обработкой.
В современном мире цифровых технологий и промышленного интернета вещей (IIoT) людям, особенно молодежи, для управления обработкой нужны ответы и четкие правила. К сожалению, во многих случаях рациональные правила отсутствуют и необходимо принять возможность непредвиденных проблем, связанных с обработкой, реагировать надлежащим образом и выбирать правильное решение.
Figure 2:
HQ_ILL_Reliable Machining And Fluid Production System.jpg
Непредвиденные проблемы и неквалифицированные сотрудники
В идеальном случае персонал предприятия обладает знаниями, навыками и опытом, которые необходимы для решения непредвиденных проблем при обработке. Однако многие производители жалуются на сложности, с которыми они сталкиваются при поиске подходящих сотрудников. Существует мнение, что обучение позволяет справиться с нехваткой квалифицированных кадров, однако некоторые производители утверждают, что обучение не приносит результатов, потому что у сотрудников отсутствует мотивация для обучения новым навыкам. Работодатели также признаются, что сотрудники, выполняющие технические курсы, уверены, что уже обладают достаточными знаниями для своей работы и не нуждаются в дополнительном обучении (см. дополнение).
Общее время производства
Анализ эффективности предприятия и устранение брака позволяют найти дополнительное время для обработки, что повышает универсальность и гибкость при соблюдении требований клиента. Общее время, необходимое для изготовления детали, складывается из времени, затрачиваемого на отдельные действия. К ним относятся собственно обработка, смена инструмента, перемещение заготовок, проверка качества, решение непредвиденных проблем, ожидание, административные задачи и др.
Некоторые из этих действий имеют ключевое значение, и их нельзя исключить (например, смена инструмента и перемещение заготовки). Помимо необходимых действий, предприятия часто тратят время на решение непредсказуемых проблем (таких, как изменения в планировании, проблемы с качеством и ожидание недостающих инструментов или материалов заготовок).
Одно из предприятий проанализировало действия, выполняемые для обработки детали, чтобы вычислить время, затрачиваемое на каждое из них (рисунок 3). Фактическое время обработки составило 15% от общего времени производства, на наладку и ожидание пришлась четверть времени, а для решения непредвиденных проблем (отсутствие или несвоевременное предоставление инструмента, остановки для удаления слишком длинной стружки) потребовались еще 25%. Сократив время на решение непредвиденных проблем, наладку, смену инструмента, ожидание и административные задачи, предприятие смогло использовать непосредственно для обработки 50% от общего времени (рисунок 4). Это обеспечило производителю дополнительную гибкость, позволяющую соблюдать особые требования клиентов.
Figure 3:
HQ_ILL_Time Spening In Machining Production Not Optimized.jpg
Figure 4:
HQ_ILL_Time Spending In Machining Production Optimized.jpg
Непредвиденные последствия экономии времени
На основании аналогичных исследований по экономии времени другое предприятие в три раза увеличило время, в течение которого шпиндель обеспечивал резание деталей. Однако при этом объем производимых деталей не вырос в три раза.
Дальнейшие исследования выявили ряд факторов, которые это объясняли. Основная причина заключалась в том, что первоначальный процесс включал в себя снятие заусенцев вне станка. В соответствии с предложениями по экономии времени снятие заусенцев на станке казалось более эффективным. Однако практика показала, что из-за новой процедуры снятия заусенцев общее время работы шпинделя увеличилось. Этот пример демонстрирует, что экономия времени для одной операции может привести к большей продолжительности или значительно меньшей эффективности другой операции.
Вывод заключается в том, что изменения режимов работы необходимо оценивать с точки зрения всего производственного процесса. Достижение баланса — сложная задача, и общих правил для этого процесса нет, за исключением одного: нужно искать методы максимально эффективного использования времени.
Изменение плана
Для достижения эффективности и универсальности необходимо непрерывно адаптировать рабочий процесс к меняющимся требованиям производства. Изменения часто происходят по внешним причинам, когда клиент изменяет конструкцию изделия или количество необходимых деталей. В результате производственному предприятию также приходится менять свои планы. Однако зачастую это влечет за собой нарушение баланса, полное рассогласование действий производителя и другие негативные последствия.
Если планирование не организовано, предприятия отправляют заготовки по цехам случайным образом и распределяют их на любые свободные станки, что создает дополнительные трудности. Проблемы планирования разрастаются подобно эпидемии. За короткое время небольшое нарушение может дать значительный эффект. И, подобно лечению эпидемии, устранить такие проблемы бывает очень сложно.
Резервное оборудование
Один из способов быстро повысить эффективность и адаптивность заключается в приобретении резервного оборудования. Большинство предприятий незнакомы с этой концепцией, а финансовые отделы готовы инвестировать средства в новое обрабатывающее оборудование, но требуют, чтобы оно не простаивало. Они рассматривают станок как инвестирование одного или двух миллионов евро (или долларов) и не понимают, почему запасные станки не используются на регулярной основе. В действительности резервное оборудование дает предприятиям весомое преимущество: удовлетворенность клиентов. Запасные станки обеспечивают гибкость и упрощают решение непредвиденных проблем.
В некоторых случаях предприятие не закупает резервные станки и работает на имеющемся оборудовании, а при слишком большом объеме работ нанимает субподрядчика. Но если у субподрядчика тоже много заказов и не хватает сотрудников, ответственность переходит к сторонней организации. Очень сложно убедить предприятия приобрести резервное оборудование, которое с большой долей вероятности будут использовать достаточно редко.
Длительная или своевременная поставка
Необходимость своевременной поставки может продлить фактическое время производства. Если производство в нормальных условиях занимает неделю, но клиенту нужна абсолютная гарантия своевременной поставки, предприятие может назначить двухнедельный срок исполнения заказа, чтобы обеспечить запас времени. В другом случае, если клиенту требуется одна деталь к определенной дате, предприятие может произвести два экземпляра (запасная деталь будет нужна на случай непредвиденных проблем с первой). Такие решения приводят к значительным потерям времени и средств и увеличивают стандартные сроки поставки.
Многофункциональные решения
Для повышения эффективности и гибкости работу предприятия можно автоматизировать с помощью многофункциональных станков с накопителем спутников. Автоматизированный модуль быстро выполняет замену в зависимости от операции и использует накопитель спутников для будущих наладок. Такую систему можно создать на базе автоматизированного многофункционального станка со спутниками для обработки деталей и магазином с несколькими инструментами. С помощью этого оборудования персонал дневной смены сможет настраивать станок и спутники для обработки различных деталей, а ночная смена будет производить детали. Это решение, однако, является достаточно дорогим, и н е все компании готовы к таким инвестициям.
Препятствия на пути к многофункциональности
Организационное препятствие на пути к многофункциональности заключается в том, что заводы обычно размещают станки в зависимости от функций (например, только фрезерная обработка, только токарная обработка и т. д.). Чаще всего оптимальной является организация станков в отсеки, где каждая группа станков обеспечивает определенные технологические возможности, применимые для определенных групп или типов заготовок. Группирование станков по функциям ограничивает возможности персонала (например, оператор токарного станка или оператор фрезерного станка). Когда операторы обучаются многофункциональности и навыкам работы со станками разных типов, предприятие становится более гибким при распределении внутренних ресурсов.
Заключение
В настоящее время эффективность производства подразумевает особое внимание к удовлетворенности клиентов и поиск оптимальных способов обработки деталей. Производителям необходимо находить баланс между прибылью и усилиями по обеспечению своевременной поставки. Оптимизация операций, эффективный контроль качества деталей и процесса, планирование с учетом производства в целом и постоянный анализ временных затрат позволяют выделить значительное количество времени для обработки деталей и повысить гибкость и производительность.
(Дополнение)
Стремление к эффективному производству
По мере развития производственных стратегий операторы сталкиваются с новыми задачами. Высокоавтоматизированные станки, интуитивно понятное программное обеспечение и современные режущие инструменты позволили уменьшить число обязанностей операторов. К сожалению, использование такой сложной технологии производства часто приводит к тому, что некоторые сотрудники переоценивают свои рабочие навыки.
Многие производители обнаружили, что сотрудники не проявляют энтузиазма и утверждают, что обладают достаточными навыками, когда им предлагают пройти профессиональное обучение. Такой образ мышления не позволяет им расти и развиваться в новой производственной среде.
Во Фландрии есть поговорка: "Не стоит давать сове свечу и очки для чтения, потому что она не умеет или не хочет читать". В США есть другая пословица: "Можно пригнать коня на водопой, но пить его не заставишь". Человеку можно предоставить все необходимые средства для достижения цели, но если у него нет желания, все усилия будут напрасны.
В настоящее время большинство предприятий используют эффективное аппаратное обеспечение, инструменты и программы обработки. Таким образом, человек стал важнейшим элементом в обеспечении эффективного производства. Наряду с перспективным мышлением, сегодня также необходимо обладать способностью анализировать процесс обработки. Это умение подразумевает не работу за компьютером, а непосредственное наблюдение за процессом.
Это позволит многое понять о состоянии процесса — так же, как человек может по биению сердца понять, правильно ли оно работает. Это понимание мы получаем не с помощью универсальной формулы. Важно знать, что отслеживать и какие благоприятные факторы влияют на производство. Компания Seco предлагает свои поддержку и опыт, а также предоставляет разные виды технического обучения. Если сотрудники предприятия обладают подходящим образом мышления, Seco поможет им получить новые знания и научит эффективно применять навыки.
Автор:
Патрик де Вос (Patrick de Vos), менеджер по развитию бизнеса и техническому обучению консалтинговой службы Seco
Компания Seco Tools, головной офис которой находится в г. Фагерста, Швеция, и которая представлена более чем в 75 странах, — это ведущий мировой поставщик решений для фрезерования, токарной обработки, обработки отверстий и инструментальных систем. Уже более 80 лет компания предлагает технологии, процессы и техническую поддержку, в которых нуждаются предприятия для получения максимальной производительности и рентабельности. Подробную информацию о том, как инновационная продукция и профессиональная поддержка компании Seco приносят успех производителям в различных промышленных сегментах, читайте на сайте www.secotools.com.
Еще больше новостей | ![]() |