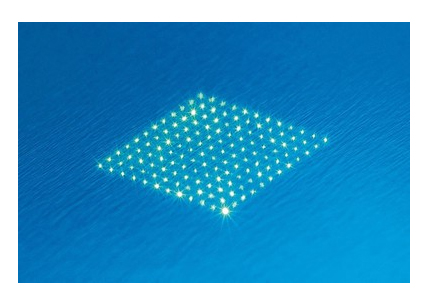
Гибридный производственный процесс лазерной резки тонкостенных металлических полос позволяет изготавливать даже мельчайшие контактных детали экологически чистым, высокоточным и эффективным способом.
Изображение: Fraunhofer ILT
От этих крошечных деталей зависит использование современного транспортного: мы говорим о нескольких тысячах разъемов в автомобиле, через которые протекают сигнальные и управляющие токи. До сих пор эти контактные детали производились, например, в Kostal Kontakt Systeme в Люденшайде с использованием классического процесса штамповки и гибки. Однако испытанный механический процесс уже достигает своих пределов, потому что из-за увеличения количества соединительных элементов существует потребность в их миниатюризации. Кроме того, контактные части имеют все более филигранную структуру. В частности, при создании контактных площадок с несколькими независимыми упругими контактными точками на очень маленьком пространстве лазерная резка открывает возможности дизайна, которые ранее было невозможно реализовать. Резервирование точек контакта поддерживает электрическую надежность, необходимую для передачи сигнала, несмотря на самые маленькие контактные системы.
Еще одно дополнение - спиральное сверление с использованием лазеров ультракоротких импульсов (лазеры USP): запатентованный процесс Института лазерных технологий им. Фраунгофера ILT уже зарекомендовал себя в прецизионном микро-сверлении с большим соотношением сторон в стали, стекле и керамике. Точность говорит в пользу спирального сверления: диаметр фокуса составляет 25 мкм - с шероховатостью Ra на стенках скважины менее 0,5 мкм. Высокое качество достигается только при низких скоростях процесса.
Но можно ли использовать проверенный процесс для резки деталей из листового металла? Как можно увеличить скорость процесса, чтобы его можно было использовать и в серийном производстве? Помня об этом, Kostal и Fraunhofer ILT начали совместный проект ScanCut с Amphos и Pulsar Photonics из Херцогенрата, который был завершен в феврале 2020 года на средства Европейского фонда регионального развития (ERDF) и земли Северный Рейн-Вестфалия. «В этом проекте мы использовали нашу спиральную буровую оптику вместе с многолучевым модулем от Pulsar Photonics GmbH и мощным источником луча от Amphos GmbH», - объясняет Ян Шнабель, научный сотрудник группы микро- и наноструктурирования Fraunhofer ILT.
Компания Amphos разработала мощный источник излучения на основе технологии InnoSlab с выходной мощностью 300 Вт и энергией в импульсе 3 мДж. Высокая энергия импульса необходима, когда лазерный луч разделяется на 20 отдельных лучей. Но сначала партнеры по проекту проверили, работает ли многолучевой подход в тестах с двух- или шестикратным делением лучей.
В последующем проекте Pulsar Photonics и Fraunhofer ILT намерены продолжить разработку технологии спиральной резки с использованием многолучевого подхода; знания, полученные в проекте по разработке источников пучка большой мощности, тбудут использованы для расширения портфолио Amphos.
Особое внимание партнеры проекта уделили автоматизации. «Мы внедрили электрически регулируемые держатели зеркал и оптики для автоматической регулировки положения луча», - говорит Шнабель. Теперь, благодаря запрограммированному алгоритму, регулировка оптики спирального сверления может быть запущена одним нажатием кнопки.
Еще больше новостей | ![]() |