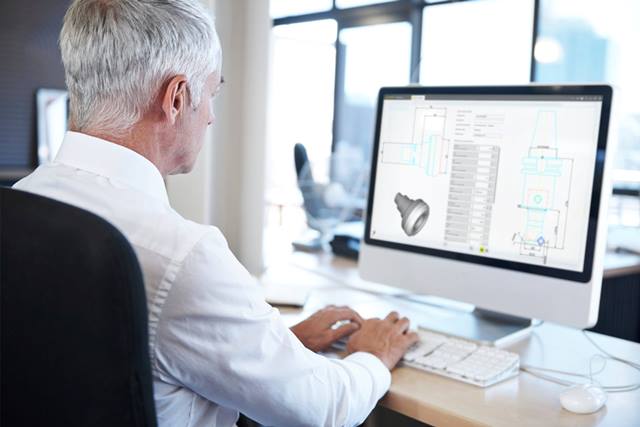
В местечке Хегбо, недалеко от Стокгольма, на празднование 75-летия компании Sandvik Coromant съехались около 50 журналистов из 18 стран. В течение двух дней руководители основных подразделений компании презентовали последние технологические разработки.
О разработках Sandvik Coromant в сфере аддитивного производства рассказал руководитель одноименного подразделения Микаэль Шуйски. В структуре компании создан инкубатор, специализирующийся на развитии 3D-печати. В Sandvik Coromant уже отработан полный производственный цикл аддитивного производства – от выпуска порошка до конечной продукции. Проведенные компанией тесты показали, что выпущенная методом аддитивного производства продукция на 60% легче, чем - выпущенная традиционным методом. А использование четырехлучевых лазеров позволит снизить затраты аддитивного производства в десять раз. Sandvik Coromant намерена развивать производство не только инструмента и пластин методом аддитивной печати, но и производить готовые детали для клиентов.
Магнус Экбяк, глава подразделения Развития бизнеса, представил стратегию компании по внедрению технологий Industry 4.0. Он отметил ключевые принципы 4-й промышленной революции: взаимосвязь машин, цифровые "близнецы" физических объектов, автоматизация и автономность. По его мнению, уже к 2025 г. стоимость рынка металлорежущего инструмента будет наполовину составлять программное обеспечение. Компания уже производит линейку инструмента CoroPlus, оснащенного сенсорами, передающими по Bluetooth информацию о выполняемом процессе и состоянии самого инструмента. В режиме реального времени информация поступает от инструмента к оператору, который может "на ходу" вносить изменения в процесс. Эту концепцию вы сможете увидеть уже в ближайшее время на выставке "Металлообработка 2017".
Sandvik Coromant уже использует принципы Industry 4.0 в своем собственном производстве пластин на заводе в г. Гимо (Швеция). Местное производство было основано в 1951 г. и с тех пор непрерывно модернизируется. Сейчас завод работает в три смены, работа в ночную смену происходит без участия человека. Информация о движении в производстве каждого заказа в режиме реального времени отражается в облачном сервисе. С его помощью менеджмент предприятия определяет наиболее эффективную загрузку произодственных мощностей. Если какой-либо станок не работает в течение 60 мин, он автоматически переходит в режим ожидания для экономии затрат на электроэнергию. На заводе запрещена фотосъемка, так как ряд роботизированных станков уникальны и разработаны компанией именно для этого завода. Доставка из одного цеха в другой осуществляется автономными машинами. Интресно, что все автомобильные парковки вокруг завода оснащены зарядными устройствами для электромобилей.
Еще больше новостей | ![]() |